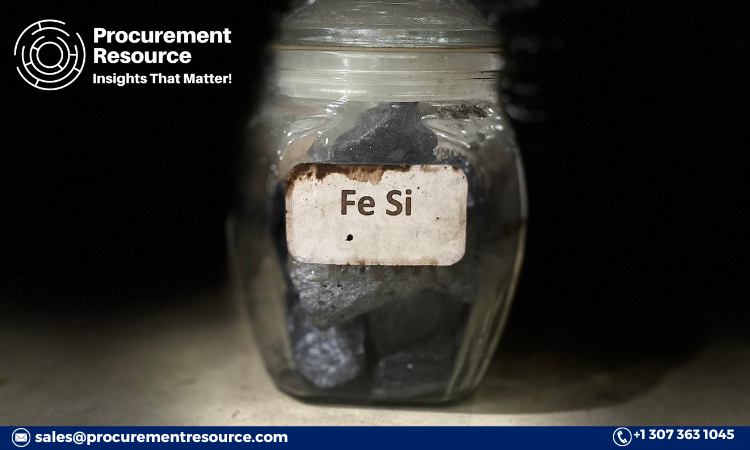
Ferrosilicon Production Process Report: A Comprehensive Overview
Ferrosilicon is an essential alloy widely used in various industrial applications, particularly in steel production, casting, and chemical industries. It is an alloy of iron and silicon, typically containing between 15% to 90% silicon by weight. The ferrosilicon production process is critical because the quality and composition of the alloy directly impact the effectiveness and efficiency of the industries where it is applied.
This blog will provide a detailed overview of the ferrosilicon production process, from raw material selection to final product packaging, emphasizing the key steps, challenges, and innovations that drive the production of this vital alloy.
Key Raw Materials for Ferrosilicon Production
The ferrosilicon production process begins with the careful selection of raw materials. The primary ingredients include:
- Silica (SiO₂): This is the primary source of silicon in ferrosilicon production. High-purity quartz or quartzite is often used for this purpose.
- Iron: Iron scrap or iron ore is typically utilized as the iron source in ferrosilicon production. The amount of iron varies depending on the required silicon content in the final alloy.
- Reducing Agents: Carbon-rich materials such as coke, charcoal, or coal are used as reducing agents to help extract silicon from the silica.
- Fluxes: In some cases, fluxing materials like limestone may be added to facilitate slag formation and improve furnace efficiency.
The quality of these raw materials directly influences the yield and purity of the ferrosilicon produced. Therefore, selecting the right raw materials is crucial for ensuring optimal production conditions and alloy quality.
Request For Sample: https://www.procurementresource.com/production-cost-report-store/ferrosilicon/request-sample
Ferrosilicon Production Process
The ferrosilicon production process typically takes place in electric arc furnaces (EAFs) or submerged arc furnaces (SAFs). The furnace type and size depend on the production scale and the silicon content required. Below is an overview of the key steps involved in the production process:
1. Mixing and Pre-treatment of Raw Materials
The first step in the ferrosilicon production process involves mixing the raw materials in the correct proportions. The silica, iron, and reducing agents are weighed and blended thoroughly to ensure even distribution of the components. In some cases, pre-treatment such as drying or calcining of the materials is necessary to remove impurities and moisture.
2. Charging the Furnace
Once the raw materials are ready, they are charged into the furnace. In the case of submerged arc furnaces, the electrodes are submerged into the material charge, creating an electric arc. The high-temperature arc (typically between 1,500°C and 2,500°C) is required to reduce the silica and form the ferrosilicon alloy. The following chemical reactions occur:SiO2+2C→Si+2COSiO₂ + 2C \rightarrow Si + 2COSiO2+2C→Si+2CO Fe2O3+3C→2Fe+3COFe₂O₃ + 3C \rightarrow 2Fe + 3COFe2O3+3C→2Fe+3CO
These reactions result in the formation of molten ferrosilicon and carbon monoxide (CO) as a byproduct.
3. Refining and Tapping
As the furnace heats up, the ferrosilicon begins to form at the bottom of the furnace. The alloy is denser than the surrounding slag, allowing it to settle at the base. Refining takes place as impurities, such as oxides and unwanted elements, rise to the surface and form slag, which is then skimmed off.
Once the desired silicon content and alloy composition are achieved, the molten ferrosilicon is tapped from the furnace and cast into molds for cooling. The ferrosilicon solidifies into blocks or granules, depending on the cooling method used.
4. Crushing and Sizing
After cooling, the ferrosilicon is broken down into smaller pieces using crushers. The alloy is then sized according to customer specifications. Typically, ferrosilicon is available in lump, granule, or powder form, with different grades tailored to specific industrial needs.
5. Packaging and Distribution
Once sized, ferrosilicon is packaged in bags or containers for shipment. Proper packaging is critical to prevent contamination and ensure the alloy maintains its quality during transportation and storage.
Challenges in Ferrosilicon Production
Despite being a well-established process, ferrosilicon production poses several challenges:
- Energy Intensity: The electric arc furnace process is energy-intensive, requiring substantial amounts of electricity to maintain the high temperatures necessary for production.
- Environmental Impact: The generation of carbon monoxide and other greenhouse gases is a significant environmental concern. However, recent advancements in carbon capture and recycling technologies are helping mitigate this issue.
- Raw Material Quality: Variations in the purity of raw materials, especially silica and iron, can affect the final product’s consistency and quality, leading to inefficiencies or the need for additional refining steps.
- Furnace Maintenance: The high temperatures and harsh conditions inside the furnace can lead to wear and tear on equipment, necessitating regular maintenance to avoid production downtime.
Innovations in Ferrosilicon Production
Advancements in technology and process optimization are helping to make ferrosilicon production more efficient and sustainable:
- Energy Efficiency Improvements: Innovations such as improved furnace design, energy recovery systems, and the use of alternative energy sources like solar and wind power are reducing the energy footprint of ferrosilicon production.
- Recycling of Byproducts: Carbon monoxide, a byproduct of the production process, can be captured and used as a fuel source or raw material for other chemical processes, reducing waste and improving overall efficiency.
- Automation and Process Control: Modern ferrosilicon plants employ advanced automation and process control systems, allowing for precise monitoring of production parameters and more consistent product quality.
The ferrosilicon production process is an intricate combination of chemistry, engineering, and resource management. While it presents challenges such as high energy consumption and environmental impact, ongoing innovations are making it more sustainable and efficient. With continuous improvements in raw material sourcing, furnace technology, and waste management, the ferrosilicon industry is well-positioned to meet the growing demands of the steel and casting sectors while minimizing its ecological footprint.
Contact Us:
Company Name: Procurement Resource
Contact Person: Endru Smith
Email: sales@procurementresource.com
Toll-Free Number: USA & Canada - Phone no: +1 307 363 1045 | UK - Phone no: +44 7537 132103 | Asia-Pacific (APAC) - Phone no: +91 1203185500
Address: 30 North Gould Street, Sheridan, WY 82801, USA